Is your manufacturing operations process lacking in productivity, profitability and people that champion your brand?
Is your manufacturing operations process lacking in productivity, profitability and people that champion your brand? Maybe your equipment is aging or your team lacks training on current processes? Then this article is for you...
4 Smart Ways To Effectively Approach Manufacturing Operations Management
When you’re in the business of making your own products to sell - whether it’s at retail or to other businesses - efficiency is everything.
Your team's efficiency determines how much of the labor you do or do not need, and how much turns into products one can see. The more inefficient your business, the fewer products you will get out of the labor put in.
For that reason, it’s important to keep in mind the relationship between productivity and operation costs. Your goal should be make the right steps toward consistently improving your workflows.
Let's discuss the vital principles of efficient manufacturing operations...
Lean
You can’t really talk about efficiency in manufacturing without talking about lean principles and techniques. Though these principles have gone on to be used in many different industries, they started with lean manufacturing.
This is effectively a set of steps you take to improve productivity by first sorting your materials and work resources to ensure clean workflows. Then, cleaning areas and keeping them as fit-for-purpose as possible. Followed by standardizing your work processes so that they are easily replicable time and time again.
Inventory Management
Lean manufacturing encourages you to:
- Sort your materials
- Eliminate items you don’t need
- Improve access to resources you do need
Optimal manufacturing inventory management systems can help you go even further. With these, you can track the specific resources and materials that you have on hand so that you’re always able to see when it is time to re-order and when you’ve ordered too much.
In turn, you and your team can correctly manage future orders to ensure adequate space for all needed materials. Inventory software can also help you quickly locate materials and resources when you have unexpected urgent need.
Equipment Effectiveness
Maintaining the maximum operational effectiveness of your machinery is imperative for ensuring that you’re able to meet production goals.
Preventative maintenance is important, but predictive maintenance goes a step further. By learning which parts of your machinery are likely to fail first, and finding the right replacements for them, such as precision angular contact ball bearings for CNC machines, you can make the repairs and replacements much more quickly when they happen.
This can minimize downtime as much as possible, allowing your machines to quickly get back online. Training your team on operating the machines and troubleshooting them as well so that you don’t have to keep going out-of-house with contractors when there’s equipment trouble.
Manufacturing Operations Training
Continuous training should be a part of every manufacturing operation. Not only should you provide the safety and work process training that helps you keep your standards high, but you should also look at the benefits of cross-training.
If you have one person who is able to use a machine that is essential for your operation, losing that person -- even temporarily -- can halt production and cost you in several ways. Cross-training provides you predictability in manpower to temporarily fill team leaders' shoes when they are absent.
0 Replies
Like what you see? We've been told our blog posts are like potato chips: You can't read just one...
Subscribe to receive them fresh in your Inbox, and you can grab our best insights about social media marketing before everyone else sees it!
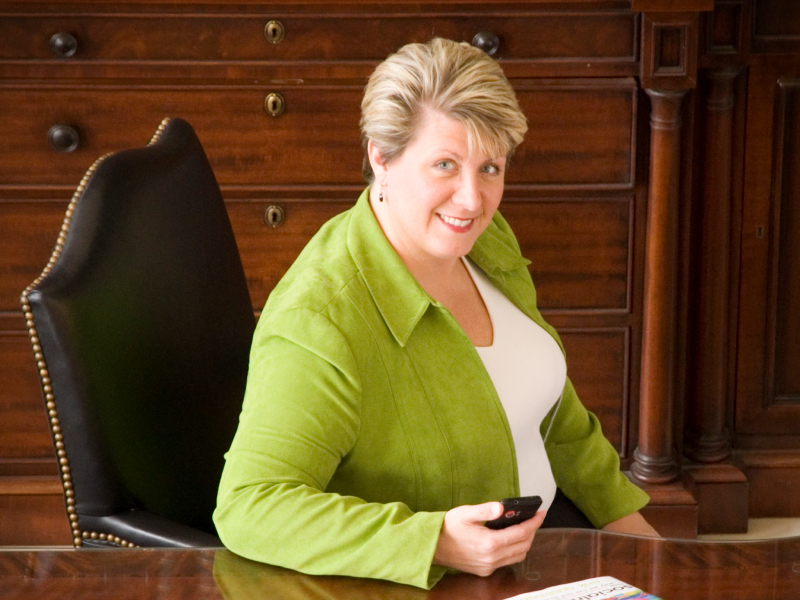
Relevant Resources
view allThe True Cost Of Letting Peak Sales Periods Pass You By
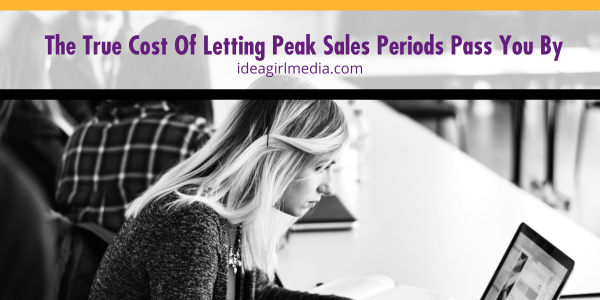
Three Surprising Signs You’re Still Silencing Your Female Employees
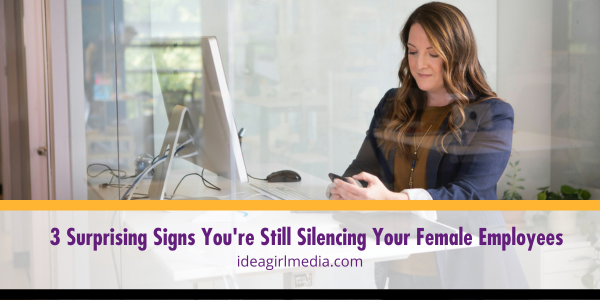
How Ongoing Training In The Workplace Can Drive Long-Term Business Growth
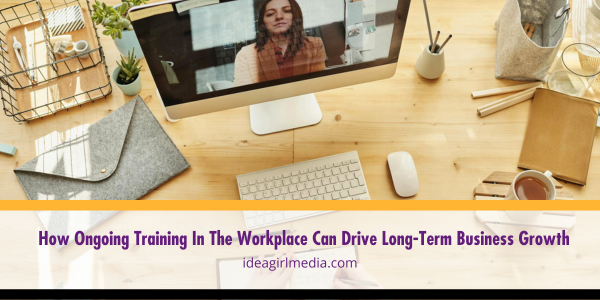
Leave a Reply